上膠運用中的電暈處理
按照生產線速度給紙張、膠片、金屬化薄膜及箔紙上膠并保持高質量涂層要求提高基質表面附著力。電暈處理可以提高黏合點并增強表面附著力,同時不會犧牲基質本身特性。在上膠運用中,電暈系統設計經歷顯著的變化來適應更輕卷材,更高生產線速度操作和更先進的基材。發展的范圍包括要求處理導電基板、電暈輥筒壓合,將電暈輥筒作為“拉輥”使用,修改電暈基站設計減少褶皺或“背面”電暈。已經嘗試使用幾種技術來適應導體基質并減少褶皺和“背面”電暈機會。另一個方式:雙電極/覆涂輥筒科技,被目前認為是克服此類問題主要方式。我們曾經討論了多種技術,目前現階段設備中使用的技術是控制參數及上膠運用。
設備基礎:電暈處理基站
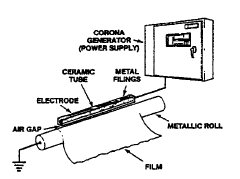
圖1—光輥站(陶瓷電極)
在80年代,電暈處理站的研發使得電極和基站都發生革命性的改變。光輥設計革命性改變的基本是起初成功地將電暈輥上的絕緣包覆轉移至電暈電極(圖1)。這類改變包括第一次將陶瓷作為電介質。但在那時候用陶瓷包覆在技術上并不可行。這就允許基站“開放”設計但同時為操作員提供電擊安全防護。同時也允許基站可以處理導體基質和非導體基質。在那個時代此類優點被廣泛認同。
比較不為人們所知的是同時出現的電極組件,將臭氧排放位置從一個封閉的基站周邊移至電極裝置的尾部。這種新的方式使得電極裝置旋轉允許卷材黏接通過.不再需要機體去捕捉和儲存排除的臭氧。相反,臭氧在氣隙產生部分即立刻捕捉被排除。但是在當時這種改變并不為人們認同,但是卻有著顯著的優點。這極大的降低了臭氧進入工作區的機會,并使得包覆輥基站的構建設計開放。
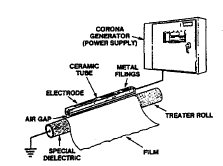
圖2-光輥雙絕緣基站(陶瓷電極,包覆輥筒)
光輥雙絕緣基站是今年來的一大發展,極大地擴展了光輥基站能力。雙絕緣基站(圖2),不僅將特制陶瓷涂層包覆在輥上,同時還帶有陶瓷電極、匹配或提高處理效率和其他系統的效用
除一點外,光輥雙絕緣基站具有原光輥基站所有的優點,這一點便是這種特制涂層很少需要更換或維護。然而,與傳統的包覆輥筒基站不同的是,雙電極基站在絕緣覆涂層變凹陷、有裂縫或是有針孔時仍能使用,由于電極也是陶瓷包覆,基站可以繼續電暈處理。雙陶瓷操作在操作分享時可以釋放熱力,這是其另一個優勢,因此,不管是電極還是輥包覆層都可以處于同水平的熱力釋放與包覆輥基站釋放熱力一致。這樣最終可以增加包覆輥的長期操作性能
光輥雙絕緣基站比光輥和包覆輥基站具有額外高度顯著的優勢。雙絕緣基站大大降低了超輕材質的褶皺機率同時減少了不受歡迎的“背面”處理,即在本應處理表面的反面電暈。
電暈處理輥筒驅動和壓合
設備或基質特性決定了是否驅動或壓合電暈處理輥筒,而不是技術電暈要求。例如,處理基質,尤其是在極低張力下對超輕量基質處理,這些基質在電暈放電時容易褶皺更易變得嚴重。褶皺不僅造成纏繞卷質量問題,而且同時造成卷材背面處理,最終與成品無益。
可以通過增加纏繞量和電暈輥上基材張力來減少褶皺和隨之而來背面處理。對于輕微起皺問題這就足夠了。而對于較嚴重褶皺問題,在膠片進入基站的電暈輥上增加壓輥可以減少或緩和此問題。增加壓輥要求電暈輥被驅動,要求輥上有驅動軸。此時可能需要一個完全重建或是替換基站
若在您運用中可能會出現褶皺,需要提前計劃并預留增加壓輥空間,即使您沒有現成可安裝的壓輥。在此情況下,還需在電暈處理輥筒上增加一個驅動軸。
大多數電暈處理基站并非要求電暈輥被驅動,因此,大部分基站沒有配有驅動軸。即使是輕基質也提供充足摩擦和張力以線速度旋轉輥筒。即使輥筒在基質移動基電暈器電源關閉的情況下無法旋轉,輥筒也可以在電暈電源通電時旋轉。此累現象被視為電氣銷,并被工廠利用稱其為靜電銷桿,但它并不接近機械壓輥的效果。他們真正的優勢在于他們較小可以在設備安裝后輕易加入
由于電暈放電提供膠片電氣銷至電暈輥筒上,也許有人會說“為何不可阻止褶皺”。此答案是即使電暈放電可以提供釘電源,但在許多情況下,釘電源伴隨著而來的是造成膠片褶皺的靜電力。褶皺甚至會在輥筒未能按照與線速度相匹配的速度旋轉的情況下加劇。驅動輥筒因此將會減少褶皺發生的可能。
旋轉電暈輥筒,且在某些情況下要求增加壓輥,尤其是在操作高度延展性的基質時,此類基質要求高度同樣且在整個過程中要求緊緊控制張力。利用基質驅動電暈輥可能造成基站兩端不平衡,但此種不平衡足以延伸基質。在某些情況下,設備設計還要求電暈基站作為拉輥。這就要求電暈輥被壓合且驅動并為設備提供某種張力控制點
電源
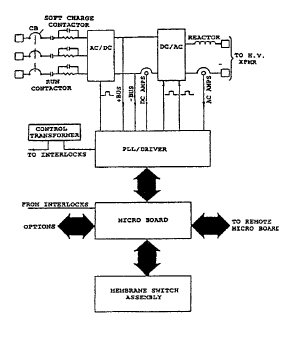
圖3-電源圖
所有的電暈處理設備要求控制電氣電源。低壓60赫茲電源被供給至一個電氣設備中用于提高頻率。高頻電源被運用至升壓變壓器中用于提高電壓。高壓、高頻率電能放通過電暈至接地鋼輥的卷材中釋放電極。
盡管基本原理不變,在過去30年中,已經有許多的進步,大大的增強了電源性能能力。最早的電源是通過電動發電機供電,被證明由于機器衰竭并不適用于長時間連續操作。此類早期電源被使用特斯拉線圈和火花隙帶動的電源替代,可產生高頻高壓電能。此類在電動發電機上的設計可謂一大進步,但是由于火花隙易腐蝕性,此電源仍有待改進。
利用晶體管作為電源輸出設備的電晶體電源后來出現。然而,早期電晶體輸出電源力極為有限,且此裝置要求16個電晶體并排連接以達到所需功率。盡管電晶體被認為是十分可靠穩固的晶體設備,但是由于所需大量設備導致隨機故障比例增加。
電源的自然演化引領利用硅可控整流器(SCR)作為電源輸出設備的逆變器發展。在過去的25年中,SCR型 的逆變器被廣泛使用,并被證明十分穩固可靠。
近年來晶體管技術的領先導向新一代電暈處理電源出現,大大提高了更小尺寸墻體中的電源輸出量。這類信絕緣柵雙極晶體管(IGBT)可以處理更高電流,且可邏輯控制提供高速的打開/關閉開關,并精確控制電暈電源和頻率。
邏輯可控功率設備的出現允許利用可編程的微處理器和微型計算機芯片,可處理各種基質的水平。電暈處理電源的控制電路的改進目前可獲得大大增加了電暈處理的持續性,加強了外擠材料至基才的黏合力,且在后處理運用中,如墨水,底涂料,覆涂至擠壓涂層面。集成微處理技術,帶著先進控制系統的處理器保證了先進控制,確保電暈處理精確度和持續性通過自動調整電源供電和聘禮至不同的變量如電極、輥類型、卷材厚度和空氣間隙(如圖3)
功率密度
電暈處理設備選擇中最顯著的設計標準是抓住系統來適應具體運用需求。電力標準以千瓦為單位,是由大部分較難處理的上膠基質決定的電暈電源決定的。電暈力是以功率密度來衡量(瓦數/平方英尺/每分鐘),這不僅僅考慮電源等級,且考慮所運用功率的時間長度。若給定的材質按照給定功率密度電暈處理,其表面附著力將按照某個量增加。這是表面處理的基本目標。然而,最終達到的表面力及增量取決于材質的起始表面附著力。例如,在PET上運用1.0功率/平方英尺/分鐘功率密度將從44DYNES 增加至48DYNES。盡管最終的DYNES比第二次嘗試要高些,但是由于起始等級不高,其增量也較小
如您所想象的一致,不同的材質對電暈處理的反應也不同。一些諸如滌綸等材質,樂意接受電暈,在相對底功率密度的情況下可以快速增加表面附著力,大約從0.5增加至1.0.爾其他的材質諸如帶有添加劑的。。。并不接受電暈,但是仍然可以在中等功率密度的情況下其表面附著力,2.0到5.0.
電暈水平,即功率密度等級,因不同運用而變化。此處所挑選討論材質和功率密度是由于其是典型的擠壓式上膠運用,然而,電暈水平還因為添加劑載重和其他基質的特性不同而明顯不同。
電暈站位置
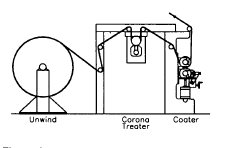
圖4
現今大部分輥覆涂是通過使用水基粘劑和涂料來完成。使用水基材質要求基材必須比溶基型涂料有更高表面附著力。因此,盡可能使用預處理基質,而預處理高分子聚合物必須在覆涂時再次處理。圖表5顯示的不同材質處理等級
圖表5– 典型功率密度
溶劑型涂料: | 1.2 to 1.4瓦/平方英尺/分 |
水基型粘劑: | 1.3 to 3.3 瓦/平方英尺/分 |
UV 涂料 | 2.0 to 3.0 瓦/平方英尺/分 |
100%固體粘劑: | 1.0 to 1.5 瓦/平方英尺/分 |
預處理和后處理
大部分高分子是在擠壓工藝中處理。處理必須保持大于44DYNS 這樣基材不會在上膠時“堵塞”。若基材含有諸如滑動或防堵塞的添加劑,則其表面附著力將降低,這是因為添加劑都游離至表面覆蓋了處理材質。當基材隨后進入覆涂工藝時,應該再次在工藝線上處理基質將恢復電暈處理甚至提高到更高處理等級。處理的密度可以高于44DYNES ,只是因為纏繞基材前,被處理的基材表面將覆蓋一層涂料或添加劑。
后處理,換言之,處理覆涂基質表面以助于后續轉換工藝,這主要是通過電暈工藝完成。預先和后處理工藝要求設備的幾種配置來滿足擠出上膠運用中廣泛不同的技術和成本要求
總結
盡管線速度日益提高,要求更輕卷材和更低張力,以及共擠基質的出現,電暈處理技術已經取得較大進步來滿足對技術和成本需求嚴格的覆涂行業表面處理工藝。
工業公司為福斯特爾撰寫